Should your trailer fleet be equipped with disc brakes? It’s no slam dunk.
The case for using air disc brakes (ADB) on trailers is pretty strong, but it’s not a slam dunk. They do offer better performance, but standard drum brakes already do a perfectly adequate job.
The maintenance requirements are lighter, but the service intervals are critical. And the cost/weight delta between drums and discs is no longer a big sticking point. So why aren’t more fleets making ADB the standard trailer spec’?
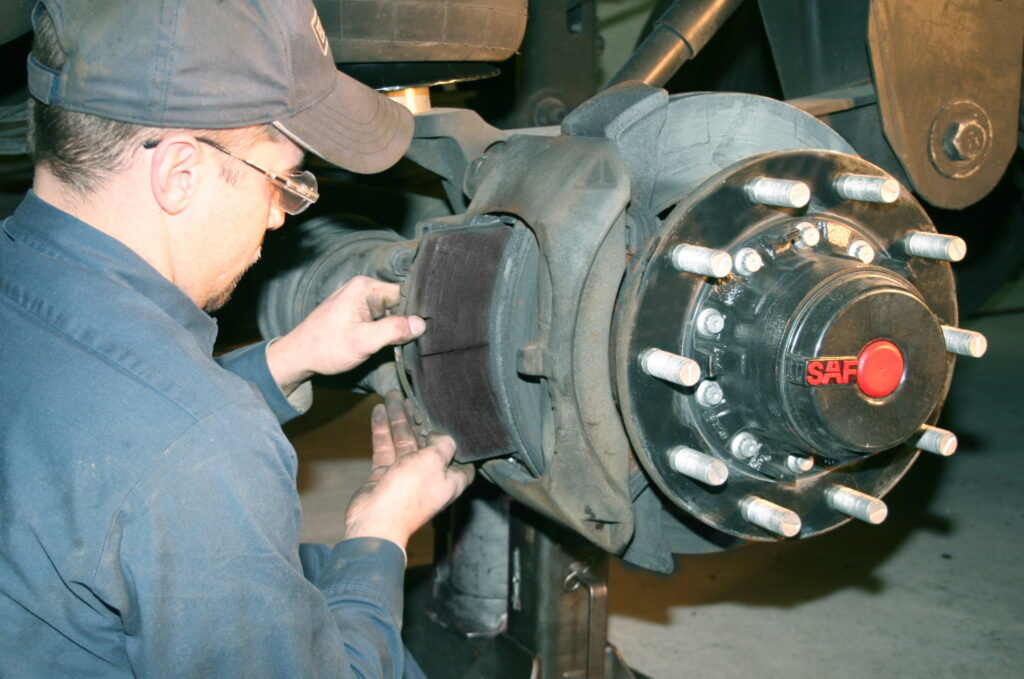
As it turns out, more fleets are jumping on the ADB bandwagon.
Suppliers typically don’t share insights on penetration rates publicly, but during a disc brake study group session at the annual meeting of the ATA’s Technology & Maintenance Council in New Orleans, panelists shared ADB uptake rates for tractors and trailers.
By the end of 2023, market penetration for tractors had soared to 50% while trailers were mired at 15%. More important than the percentage of market share was the pronounced upward trajectory of both types of ADB.
Trailer ADB were less than 5% as recently as 2011. Uptake was almost flat through 2016, when growth took off. Market share for ADB in 2023 was 15% and climbing.
While more of your cohorts are embracing air disc brakes in their trailer spec’, does that mean you should too?
“The drum versus disk discussion is still a healthy one to have,” said Brian Andrews, engineering manager at Cummins-Meritor. “Should I just follow the crowd and go with aid disc brakes, or are there other things I should consider?”
ADB pros and cons
One of the oft-cited advantages to disc brakes is somewhat intangible, but very real. Disc brake fleets report far fewer brake violations and out-of-service citations related to brake condition.
Panelist Roger Maye, director of technical services for Consolidated Metco (ConMet) shared an anecdote about how law enforcement personnel approach truck inspections. It nicely makes the case for ADB for keeping brake violations in check.
“The highway patrol officers have figured out the path of least resistance in doing their jobs,” he told the audience. “There’s a lot less to inspect on an ADB-equipped vehicle. ADB fleets have told us they get inspected more frequently, but they’re not getting citations from those inspections. It’s easier for the inspector to inspect, but they’re finding less, so a fleet’s exposure is less for brake inspections.”
One of the fleet representatives on the panel, Alex Gorno, maintenance director, at Jolliet, Ill.-based GP Transco, said just 13% of his CVSA violations are brake related. His fleet is 100% air disc brakes.
“Zero per cent of our violations were for pads and rotors,” he said. “The violations were all audible air leaks, chafing hoses, etc.”
There are several metrics to consider when evaluating ADB, including acquisition cost and life-cycle cost.
Mark Holley, director of marketing and customer solutions, wheel-ends, Bendix Commercial Vehicle Systems, acknowledges upfront costs can be higher, but lifecycle costs can be considerably lower, especially with shorter trade cycles.
“Once you get to the second and third year, you will see most on-highway and over-the-road applications are TCO (total cost of ownership)-positive,” he said.
Practically no maintenance is required on ADBs, including lubrication and adjustment. Pad life is generally better than standard brake linings, but that varies by application. When a pad change is necessary, it takes a fraction of the time of a drum brake reline.
That said, it’s unwise to push the inspection and service intervals. Worn pads can damage rotors, and rotors are pricy — far more so than a brake drum.
“With air disc brakes, it is more difficult to see the friction material, especially if you’re doing a wheels-on visual inspection,” Holley said. “You have to bend over to really get in there and see the pad thickness. Some fleets are using borescopes with lights to see in there. That saves a ton aggravation — and time. Fleets can also consider pad wear sensors or continuous wear sensing as an option. That’s gaining some traction.”
And there are acknowledged problems sourcing parts due to supply chain disruptions, along with a persistent problem with ABS tone-ring corrosion.
“Tone-ring corrosion certainly is a major issue, but I know manufacturers are working on new designs, and new ways to attach the tone-rings, as well as experimenting with coatings,” Holley said. “You’ll see more of that to address this issue.”
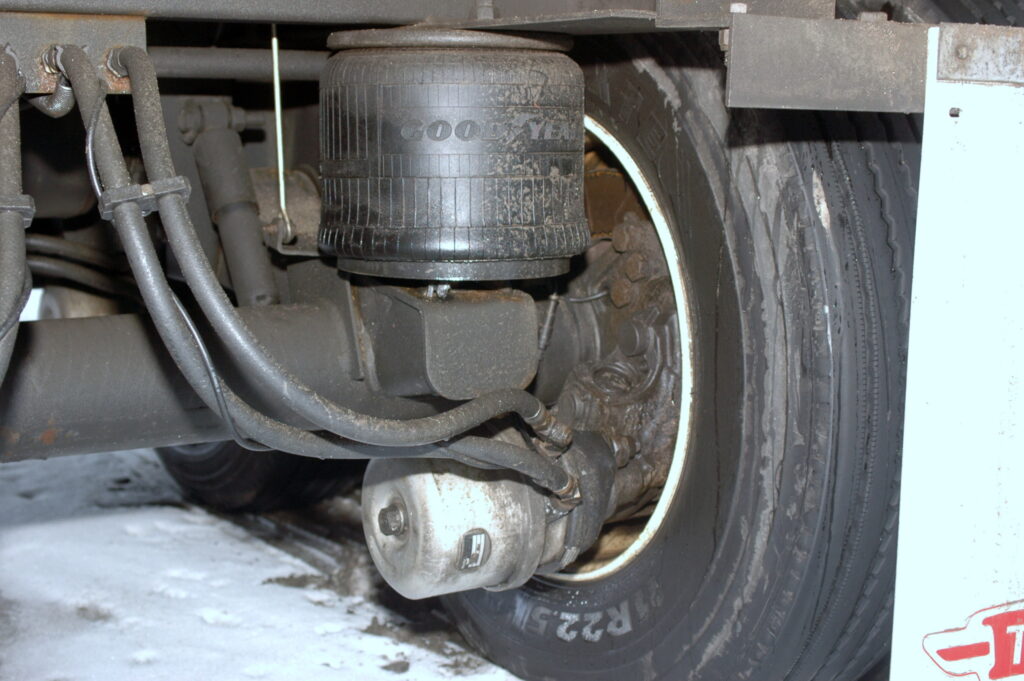
The fleet perspective
Two fleets participated in TMC’s panel discussion. In addition to GP Transco, Brent Hilton, maintenance director of Maverick, based in North Little Rock, Ark., said overall he was happy with disc brakes.
His fleet went all in on trailer ADBs in 2008 and he has never looked back. Maverick hauls fully loaded, 80,000 lb., 90% of the time. He said the main reasons for the switch from drums to disc was the “quickness” and the lower costs of the PM service as well as fringe benefits accruing from less roadside brake inspection exposure.
He also noted he has had some difficulty with supply chains as far as procuring new equipment (mostly resolved now) as well as availability and cost of parts.
GP Transco runs a seven-year trade cycle on trailers, while Maverick is at eight years. Both say most of their trailers make it through a full life cycle with just one pad change, while others may need more extensive mid-life work — a rotor replacement.
“We are capturing the benefits of increased performance of ADB, and also because of our shorter life cycle, we have reduced maintenance costs as well,” Gorno told the audience.
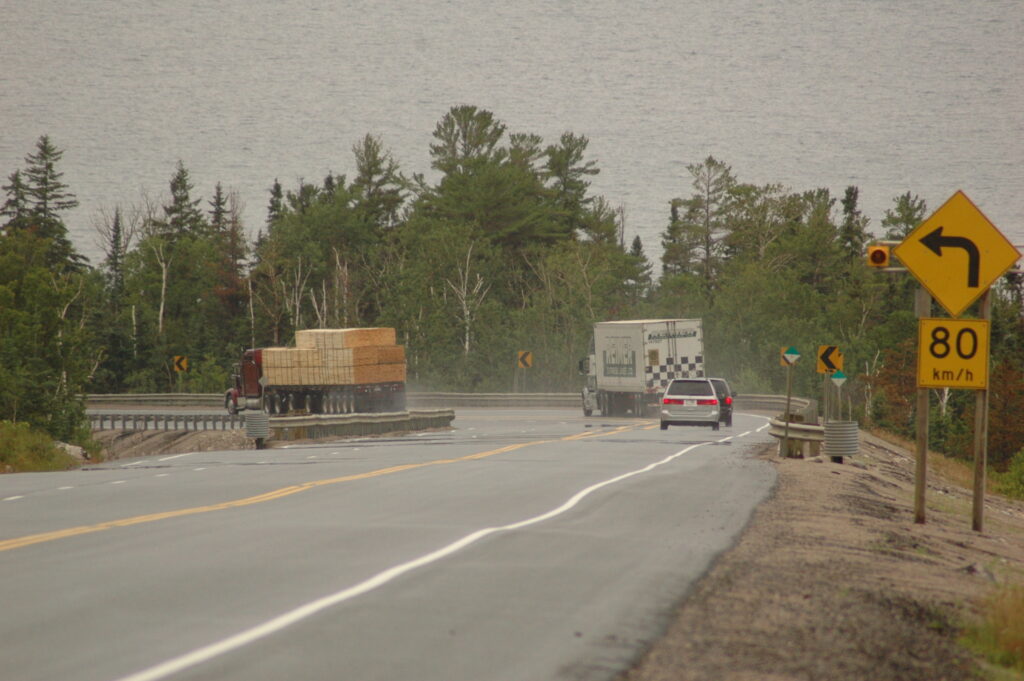
The Canadian perspective
Since Maverick and GP Transco are U.S. fleets, Today’s Trucking reached out to a few Canadian fleets for their perspective.
Ryan Blackwood, fleet services manager at Mackie Transportation told us he is all in on disc brakes for trailers, mostly for the increased stopping ability, the lower likelihood of a mechanical failure with disc compared to drum brakes, and longer service life.
“Disc brakes make vehicle inspections much easier on our drivers,” he said, “and we get a much smoother ride through the inspections stations.”
He did note that while longer service life is generally a benefit, the occasional rotor replacement can upend the life-cycle calculation.
“The sticker shock may make you think you are paying more overall, but the time between changes is much better,” he says.
Bison Transport has been spec’ing ADB on trailers for the past two years, with safety being the biggest reason for the change.
“We see the benefits from shorter stopping distances and a reduction in brake fade vs drum,” said Jeremy Gough, associate vice-president, national fleet maintenance, Bison Transport. “We have also seen no issues in our winter climate where we would see many issues with brake lining frozen to drums with conventional drum brakes.”
Driver feedback supports the continued use of air discs on trailers, he added.
“With only a few years of experience under our belt, we do see a reduction in labor needed as once wheels are removed, we can inspect the complete braking system without removing a drum,” Gough said. “We continue to service the system per the manufacturers recommendations with a goal of longer life with the air disc braking system.”
The lone hold-out in the air-disc lovefest was Erb Transport, and for justifiable reasons.
“We have not added disc brakes to our specification for trucks or trailers,” said Jim Pinder, senior corporate fleet director, Erb Transport. “The reason is two-fold: the marketplace knowledge level and parts availability in remote areas where we operate isn’t there yet. As such, the repair costs we would experience are excessive as we keep trailers in service for a very long time.”
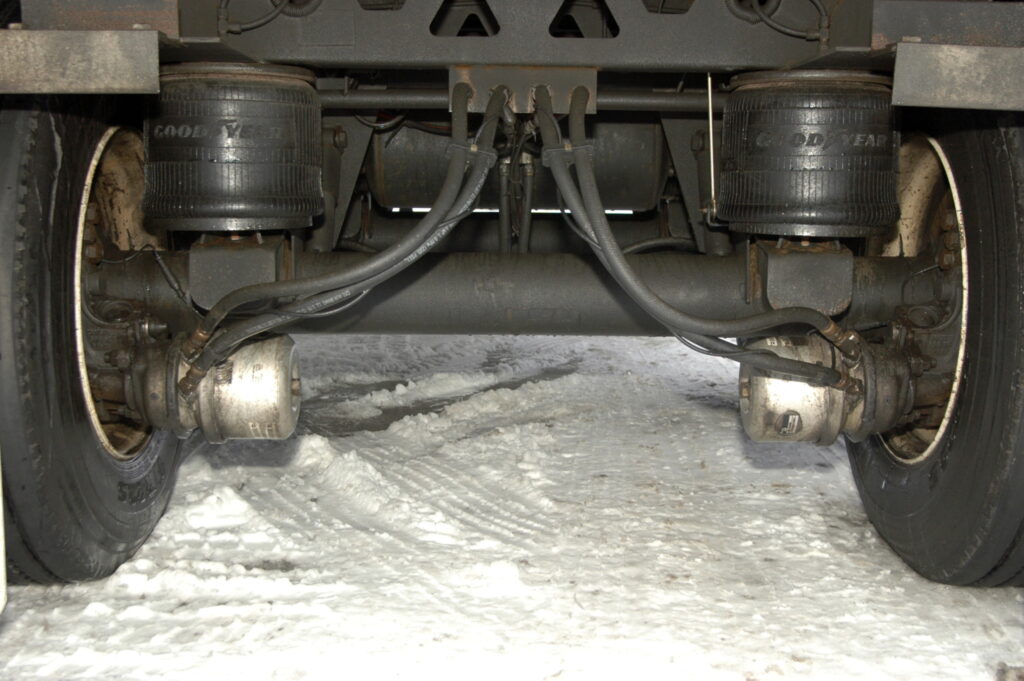
Don’t forget training
It’s fairly obvious that technicians would need to be brought up to speed on inspection and maintenance procedures. But drivers should get an update too — and maybe even the safety department.
The daily inspection requirements are different for disc brakes than for drum brakes, and drivers probably need to be taught new inspection procedures.
“While reviewing dashcam videos of hard-braking events, I noticed the ADB-equipped trucks stopped quicker, triggering a higher frequency of events.”
Chip Waterfield, Upstaging
“You wouldn’t think driver training on ADBs would be difficult, but you have to get them used to inspecting a different system,” says Chip Waterfield, fleet safety and equipment Manager at Upstaging. “ADBs do call for an extra measure of effort when inspecting the vertical caliper versus the horizontal nature of the drum brake. And they aren’t going to figure it out for themselves.”
And curiously, while drivers often comment on the smoother stops, they seldom say anything about the shorter stopping distances made possible by the faster application of the disc brakes. That, oddly enough, caused some consternation amongst drivers because they were getting more hard-braking event notifications from the safety department.
“While reviewing dashcam videos of hard-braking events, I noticed the ADB-equipped trucks stopped quicker, triggering a higher frequency of events,” Waterfield said. “One of our best professional drivers had a great observation that I don’t often hear in the ADB discussion: ‘There’s no lag in the braking effort. When you push the pedal, and the caliper responds with its grip, deceleration follows,’ the driver told me. His comments made perfect sense when compared to average-maintained drum brake equipment. There is the pedal effort, then the pushrods swing the S-cam, then the shoes [press] against the drums, and that’s if everything is in adjustment.”
Beware not to penalize your drivers by improperly citing them for hard-braking events, when it’s actually better equipment doing a better job and making the roads safer for everyone.
Have your say
This is a moderated forum. Comments will no longer be published unless they are accompanied by a first and last name and a verifiable email address. (Today's Trucking will not publish or share the email address.) Profane language and content deemed to be libelous, racist, or threatening in nature will not be published under any circumstances.
Yes, I would love to see all Class 8 Trucks along with all Trailers Mandated to be equipped with Disc Brakes. Out of Service Violations would literally be eliminated since they maintain a constant adjustment to the Braking System. Instantly, safer conditions would be achieved, so simple since Out Of Adjustment of Brakes are always the Number One Out of Service Violation.
Bruce Doyle
Hamilton
My new truck orders for the last four years are all Disc.
Excellent recap of the TMC mini tech in New Orleans. Enjoyed the read and would love to participate more in any ADB discussions.